Membrandachsanierung Dresden Hauptbahnhof
Dresden, Germany
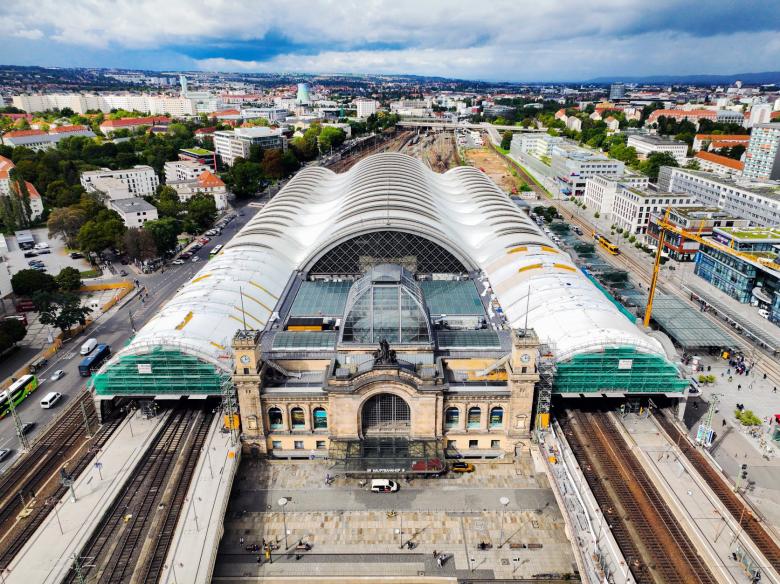
MEMBRANDACHSANIERUNG MIT SUBTILER KONSTRUKTIVER OPTIMIERUNG
Die Erneuerung der Hallenüberdachung des Hauptbahnhofs Dresden stellt mit fast 33.000 qm Fläche und einem Realisierungszeitraum von nahezu 4 Jahren aktuell eines der größten Projekte im Membranbau dar. In seiner Analyse beleuchtet Ralf Dinort, mit seinem Unternehmen IF Group verantwortlich für die Tragwerksplanung des Projekts, die neuralgischen Punkte des Bestandsdachs und wie man mit dem neuen konstruktiven Konzept die bisherigen Probleme zu vermeiden sucht. Was sich nicht geändert hat, ist sein Votum für das Membranmaterial GF-7000 von Verseidag, Teil der Serge Ferrari Group, in das er auch für diese anspruchsvolle Sanierung sein Vertrauen setzt.
VON DUNKLEN TUNNELN ZU EINEM LICHTDURCHFLUTETEN ERLEBNISBAHNHOF
Der Hauptbahnhof Dresden war Ende des 19. Jahrhunderts eine der Referenzen für Großbauten mit einer fulminanten Stahlkonstruktion, ein 3-schiffiges Stahlbindergebäude, das sich über eine Länge von 240 m erstreckt. Imposant waren die Spannweiten von 30 m für die beiden Außenhallen sowie 60 m für die Mittelhalle, zu einem großen Teil mit Glas eingedeckt und damit lichtdurchflutet wie in einem Gewächshaus. Ein Gebäude mit hohem ästhetischem Anspruch und historischer Bedeutung, welches jedoch im 2. Weltkrieg stark zerstört wurde. Während der DDR-Zeit wurden die Stahlträger mit Holz verschalt und mit Pappe, Teer und Schiefersteinen versiegelt. Die Folge war ein sehr dunkles Gebäude mit unangenehmer Tunnelanmutung. Erst nach der Wende wurde dann von der Deutschen Bahn entschieden, diesen Bahnhof von Grund auf zu sanieren, um seiner Bedeutung als einer der Landmarken von Dresden wieder gerecht zu werden.
PREISGEKRÖNTER ENTWURF MIT EINEM MEMBRANDACH
Dafür hatten die Architekten Foster+Partners einen architektonischen Entwurf kreiert, der die historische Stahlkonstruktion als Träger nutzt und eine Wellenform aufgreift, die einerseits von der Kurvatur der drei Hallenschiffe, aber auch als Bezug zum Wellenspiel der naheliegenden Elbe abgeleitet wurde. Der Baustoff textile Membran lag zu jener Zeit stark im Trend und war in aller Munde. Viele Architekten haben sich damals wie heute mit diesem faszinierenden Material auseinandergesetzt und mit seiner flexiblen Formbarkeit gespielt. Bereits damals entschied man sich – ebenso wie bei der aktuellen Erneuerung – für das PTFE beschichtete Glasgewebe GF-7000 der Serge Ferrari Group (damals noch Verseidag). Das Resultat: Man bekam eine wunderbare Leichtigkeit in den Bau und durch die herausragende Transluzenz auch sehr viel Licht in den Bahnhof, was natürlich Nutzer und Bauherrn sehr glücklich machte nach dieser jahrelangen Verdunklungssituation. Plötzlich entstand die Möglichkeit, dass alles hell wurde und man Licht bis in den hintersten Winkel bringen konnte.
CHARAKTERISTIK DES BESTANDSDACHS
Für die Textur des Daches wurde im architektonischen Konzept die Richtung der Hallenbinder aufgenommen. Dabei hat man die Bahnenrichtung der Membran, also die Kettrichtung des Gewebes, fließen lassen und die Nähte hierzu parallel zu den Bindern gelegt. Für die Architektur und Ästhetik war dies von großer Bedeutung, wuchs sich aber im Zeitverlauf zu einem Problemfeld aus. Das zweite besondere Charakteristikum für das Membrandach waren die sogenannten Trichter. Hierzu wurden Tiefpunkte so ausgebildet, dass in den Kehlen der Hallenbinder - also dort wo die Hallenfüße zusammenkommen, im sogenannten Kämpfergelenk - die Membrane dort tiefgezogen wird. Hierüber erfolgt auch die gesamte Dachflächenentwässerung von den Randzonen des Mittelschiffs und der Seitenschiffe.
2006 wurde das neue Dach in Betrieb genommen. Bereits zum Ende des Jahrzehnts zeigte sich, dass die Trichterkonstruktion nicht in der Lage war, die Schnee- und Eismassen, welche in die Trichter lawinenartig hineinrutschten, kontrolliert zu fassen und als Schmelze abzuleiten.
Die Trichter auf die Schneemassen mit ihrer Eigendynamik auszulegen, musste unabhängig von der Wahl des Membranmaterials beim Konzept für die Dacherneuerung entfallen.
Um mögliche Einflussfaktoren für die spätere Konzeption auszuschließen, wurden zusätzliche Untersuchungen angestrengt. Zur These, dass Eisschollen in die Trichter hineinrutschen und die Membrane aufschneiden könnten, oder dass Eiszapfen, die von den neu konzipierten Skylights herabfallen könnten, die Membrane durchstoßen würden, machte man im Vorfeld der Sanierungsplanung z.B. Versuche, um solche Eisfallszenarien auszuschließen. Die IF-Group entwickelte hierzu einen Test, bei dem aus 6 m Höhe angespitzte Holzpalisaden mit 12 cm Durchmesser unter verschiedenen Auftreffwinkeln auf die Membrane abgeworfen wurden. Außer einem geringen Abrieb auf ihrer Oberfläche hat die Membran jedoch keinen Schaden genommen und konnte auch nicht zerschnitten oder durchstoßen werden.
In den letzten 20 Jahren ist das Wissen um die Eigenschaften der Gewebemembrane deutlich gewachsen und Ingenieurbüros mit langjähriger Erfahrung auf dem Spezialgebiet des Membranbaus wissen um die gewachsenen Anforderungen Bescheid.
KONSTRUKTIVE OPTIMIERUNG DES MEMBRANDACHS
2018 wurde die IF Group beauftragt, ein tragfähiges Konzept für die Membrandach-Sanierung zu entwickeln. Es sollte sehr dezidiert das ursprüngliche Design von Foster+Partners Architekten respektieren. Hierzu musste man für jede Änderung, die Auswirkungen auf das Design hatte, eine Entscheidungsvorlage für Foster+Partners für deren Freigabe vorbereiten.
WAS BEDEUTETE DAS NEUE KONZEPT?
Punkt 1: Skylights zum Verschließen der Trichter
Eine Elimination der Trichter durch eine andere Formgebung war tabu. Also war die Lösung, die Trichter zu verschließen. Dazu wurden Skylights – also „gläserne Augen“ in das Membrandach integriert – mit denen diese Trichtereingänge oval und dreidimensional verschlossen wurden. Im Detail bestehen diese Skylights aus einer Stahlkonstruktion mit 3 Gurten, die auf den Hallenbindern um ihre Längsachse frei drehbar gelagert ist, da sie keine Zwängungen in die Membrane bringen sollte. Jeweils am Rand findet der Anschluss zur Membrane statt, Schnee und Wasser können also auf diese verglaste Ebene fließen. Rundum sind zentimeterbreite offene Fugen angeordnet, welche das Wasser aufnehmen. Unten an das Skylight schließt sich die Trichtermembrane an, über welche die abschließende Entwässerung sichergestellt wird. Dies bedeutet, dass die Trichtermembran von der tragenden Dachmembran entkoppelt und als Trennbauwerk das Skylight eingefügt wurde. Die Trichtermembran hat somit keine tragende Funktion mehr, sondern ist nur noch dekoratives Element sowie Entwässerungsebene, aber eben aus dem gleichen Material wie das große Membrandach. Aus der Sicht eines Reisenden vom Bahnsteig aus ist damit die Anmutung nur unwesentlich anders, als im bisherigen Bestand.
Punkt 2: Neue Ausrichtung und Formatierung der Membranelemente
Foster+Partners wollten keinerlei Montagestöße, da sie eine Einschränkung des fließenden Verlaufs und Minderung der Ästhetik befürchteten. Die Nähte verlaufen parallel zu den Bögen und wenn man dann quer dazu einen Riegel konstruiert hätte, wären dadurch die ästhetischen Vorgaben gestört. Wären jedoch die Felder in diesem riesigen Ausmaß beibehalten worden, wäre es wiederum unmöglich gewesen, diese langen Membransegmente ohne Knicke und Falten zu montieren.
Hier war die Lösung, die Zuschnittsrichtung - also die Bahnen parallel zu den Bindern - aus zwei Gründen um 90o zu drehen:
1. Sollte die starke Kettrichtung der Membran in die schneeabtragende Richtung gelegt werden, also von Binder zu Binder. Bisher gab es noch einige Felder, die seilverstärkt werden mussten, da sie in Schussrichtung ausgelegt waren, also mit ca. 15% weniger Zugfestigkeit. Die Seilverstärkung konnte jetzt entfallen. Gleichzeitig hat man jetzt von Binder zu Binder auch keine Schweißnaht mehr, welche sich schwächend auf die Zugfestigkeit der Membrankonstruktion auswirkt.
2. Parallel zu den Bindern werden jetzt keine 30 – 40 m langen Membranbahnen mehr gelegt bis die nächste Naht kommt. Im neuen Konzept sind jetzt die einzelnen Zuschnitte in der Regel auf ca. 10m beschränkt.
Hierzu Ralf Dinort: „Ein Tuch stellt ja zunächst nur eine Ebene dar. Die Form definiert sich erst durch den Zuschnitt und das Zusammenfügen. Dabei gilt: Aus je mehr Teilen ich diese 3-dimensionale Fläche erzeuge, umso genauer kann ich diese 3-Dimensionalität abbilden. Das war natürlich beim Bestandsdach kaum möglich, da man nur jeweils am Ende einer sehr langen Zuschnittsbahn - also an der Kette - etwas Material wegnehmen konnte, um die Form der Sattelfläche anzunähern. Man muss diese Approximation an die antiklastische Membranform der Sattelfläche über die Länge verteilen, sonst gibt es Gewebeverzerrungen. Das kann nur über eine starke Scherung erfolgen, bildlich mit einem rechtwinklig zueinander angeordneten Fadenverlauf zu vergleichen, der sich dann aus seiner Rechtwinkligkeit zur Rautenform verzieht. Wir haben die Bahnen kleiner gemacht und wir haben sie quer angeordnet. Das war natürlich nicht mehr genauso, wie es sich Foster+Partners ursprünglich vorgestellt hatten. Schließlich konnten wir aber überzeugen, dass diese ursprüngliche Konzeption einer wesentlichen Korrektur bedarf.“
In der Folge wurden die Einzelfelder zwischen zwei Hallenbindern in 6 Segmente geteilt. Das bedeutet pro Einzelfeld, dass sich 5 Montagestösse darin befinden sowie die zusätzliche Trichterentkoppelung.
Das Resultat sind viel kleinere Montage- und Transporteinheiten, was das Knickrisiko enorm verringert.
VOTUM FÜR GLEICHES MATERIAL: GF-7000 VON VERSEIDAG / SERGE FERRARI
Nachdem die entscheidenden Voraussetzungen geschaffen wurden, sodass die Dachkonstruktion erfolgreich geplant und umgesetzt werden konnte, stand aufgrund des vollständigen Austauschs auch die Frage im Raum, ob es eine Neuorientierung bezüglich des Materials geben sollte. Die Empfehlung von IF-Group war in diesem Zusammenhang, dass diese anspruchsvolle Erneuerung wieder mit dem ursprünglichen Membranmaterial GF-7000 realisiert werden sollte, da es das Ingenieurbüro über einen langen Zeitraum hinweg mit seiner hohen Qualität überzeugt hat. Dazu Ralf Dinort: „Wir arbeiten mit verschiedenen Laboren zusammen und haben für unterschiedlichste Projekte immer wieder die einschlägigen Versuche gemacht und auch eigene Testverfahren entwickelt: z.B. wurde im Rahmen einer Diplomarbeit ein Flexometertest entwickelt, mit dem wir ein breites Spektrum an verschiedensten Materialien geprüft haben, darunter ein sehr aussagekräftiger Doppelfalttest. Hier schnitt eben das Glas-PTFE-Gewebe GF-7000 von Verseidag am besten ab, gerade was die Resilienz gegenüber Faltungen angeht. Es war klar für uns, dieses Material auch wieder für die Ersatzüberdachung zu empfehlen. Des Weiteren haben wir Verseidag und die Serge Ferrari Group als einen Partner erlebt, der gemeinsam mit dem Ingenieurbüro an tragfähigen Details und Verbesserungen arbeitet. Wir stoßen hier immer auf offene Ohren, wenn Probleme zu lösen sind, bei Forschungsanstößen oder wenn besondere Tests zur Bestätigung von Berechnungsgrundlagen benötigt werden. Mit diesen wichtigen Faktoren in der Zusammenarbeit werden so optimale Lösungen für den Bauherrn geschaffen. Ein weiterer wichtiger Faktor war auch die hohe Transparenz der Materialherstellung gegenüber der DB Deutsche Bahn Station & Services AG von Anfang an, sei es bei Besuchen im Labor oder in der Produktion der Verseidag-Indutex unter Realbedingungen, bei dem bis ins Detail alles hinterfragt werden konnte.“
Das Votum für das ursprüngliche Material unterstützte auch einen frühen Projektstart, weil für die bisherige ZiE und UIG (Unternehmensinterne Genehmigung der Deutschen Bahn), die im Jahr 2000/2001 erstellt wurden, nur Bestätigungs- und Ergänzungsversuche durchzuführen waren und so ihre Gültigkeit behielten. Man konnte sich auf die Bestanddaten berufen, und war damit weiterhin z.B. konform zum 500 Seiten starken, sehr umfassenden Brandschutzkonzept, was bei einer neuen Materialwahl komplett neu hätte erstellt werden müssen.
BRANDSCHUTZANFORDERUNGEN AUCH FÜR DIE BAUPHASE
Für dieses Membranhallendach gefordert war ein entsprechendes Brandschutzzeugnis, was durch das GF-7000 Gewebe von Serge Ferrari Group vollumfänglich mit einem B-s1,d0 Zertifikat erfüllt wurde.
Ein wesentlicher Punkt des Brandschutzkonzepts war auch die Absicherung während der Bauzeit. Hierzu wurde das Gewebe auch in der Montagesituation betrachtet, also in Kombination mit einem Plattformnetz (Sicherheitsnetz, was 1m unterhalb der Membrane befestigt ist) und nochmals 50 cm darunter ein Staubschutznetz. Für die geplante 3 – 4 jährige Bauzeit war die Entrauchungsproblematik zu klären, weil in diesem Fall das Gesamtpaket an Schichten zu berücksichtigen ist. In dieser Kombination wurden dann Realbrandversuche gemacht und damit nachgewiesen, dass die Anforderungen mit dem Textilgewebe GF-7000 alle erfüllt werden. Ob mit oder ohne Kombination mit anderen Materialien: Beim Studium des Brandschutzkonzepts sieht man, dass sich hier die Anforderungen an die Membran wie ein roter Faden durchziehen und sehr viel darauf abgestimmt ist.
STRENGES QUALITÄTSMANAGEMENT FÜR MEMBRANPRODUKTION UND -KONFEKTION
Ein wichtiges Element für die Vermeidung von Knickfalten und Beibehaltung der Materialresilienz innerhalb Produktion, Transport und Konfektionierung der Membrandachelemente, war ein umfassendes und sehr strenges Programm zur Qualitätskontrolle, was ebenfalls eine Veränderung zum Erstbauwerk darstellte. Dazu wurden zwei unabhängige Labore beauftragt, von Seiten des Auftragnehmers Pfeifer Seil- und Hebetechnik GmbH die DEKRA in Stuttgart, von Seiten des Bauherrn Deutsche Bahn das ELLF in Essen.
Im Bauvertrag sind innerhalb des Qualitätsmanagementkonzepts eine Reihe von Materialtests mit verankert.
Zusätzlich wurde von der Deutschen Bahn nochmals eine weitere Serie an Tests gefahren, die in Belastungskammern unter verschiedenen Belastungszeiten und Laststufen einen Dauerstand simuliert. Dabei wurde im Vergleich immer unbeschadetes Material und Material mit verschiedenen Schadensbildern untersucht. Es geht also hier um das Langzeitverhalten eines vorgeschädigten Materials.
Um über alle Bauabschnitte, die sich ja über einen Zeitraum von 2022 – 2025 erstrecken eine gleichbleibende Qualität innerhalb der Produktion zu gewährleisten, werden aus jeder Produktionscharge der Membran Gewebeproben herausgenommen, mit denen umfangreiche Testverfahren umgesetzt werden.
Über Ralf Dinort, IF-Group
Dipl.-Ing. Ralf Dinort ist Geschäftsführer und Gesellschafter der IF-Group, Ingenieure für Flächentragwerke GmbH, die 1981 als Ingenieurbüro mit Kernkompetenz im Membranbau gegründet wurde. Ein Feld in der Architektur, mit dem das Büro quasi aufgewachsen ist und in der Folge sehr intensiv mit wachsender Expertise und thematischer Auseinandersetzung begleitet hat. Über die Jahre wurde das Portfolio immer weiter ausgebaut, sodass man sich heute mit sämtlichen leichten Flächen-tragwerken bis hin zu komplexen Schalentragwerken beschäftigt. Diese meist in Freiform definierten Bauwerke, werden von der IF-Group vom Entwurf bis zur Bauleitung betreut. Daneben sind Consulting und Gutachten weitere Schwerpunkte.
PROJEKTDATEN
Projekt Hauptbahnhof Dresden
Projektdauer in drei Teilabschnitten Februar 2022 bis 2025
Bauherr DB Deutsche Bahn Station & Service AG, Dresden
Projektleitung DB Station & Service AG, Dresden
Membrane Glas/PTFE-Membran GF-7000, Weiß
Gesamtfläche ca. 33.000 m² in 3 Bauabschnitten
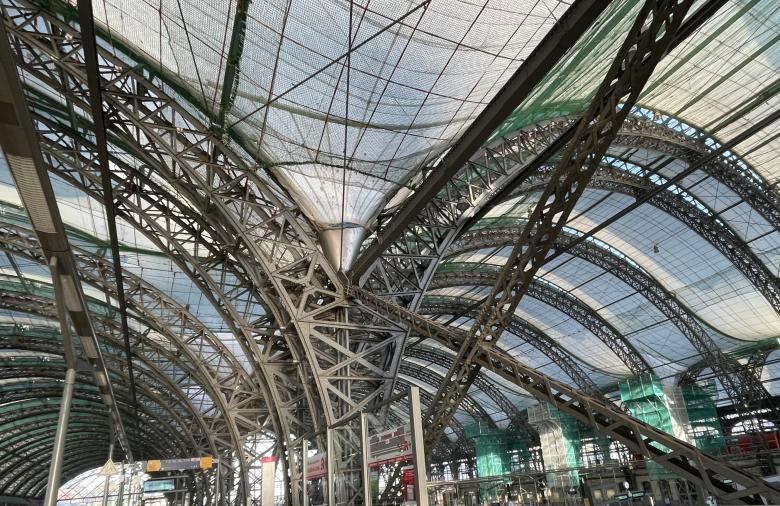
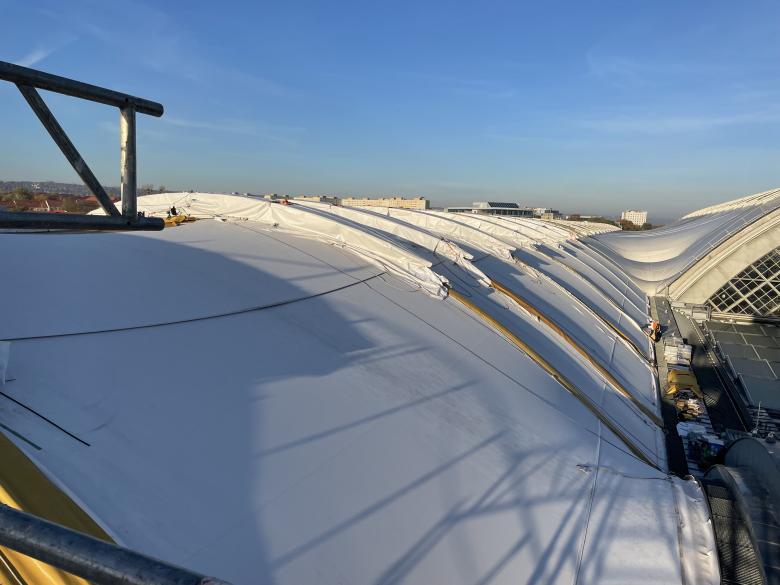
- Manufacturers
- Serge Ferrari Group
- Location
- Wiener Platz 4, 01069 Dresden, Germany
- Year
- 2024
- Client
- DB Deutsche Bahn Station & Services AG Dresden, Projektleitung DB Station & Service AG
- Entwurfsplanung Membrandach
- Foster+Partners Architects, UK
- Tragwerksplanung
- IF-Group, IF-Ingenieure für Flächentragwerke GmbH, Reichenau
- Generalplanung
- EHS Beratende Ingenieure für Bauwesen, Lohfelden
- Projektsteuerung
- Vössing Ingenieurgesellschaft mbH, Dresden
- Bauausführung
- Pfeifer Seil- und Hebetechnik GmbH, Memmingen
- Bauüberwachung
- PTB Ingenieurbüro für Planung, Technologie und Bauüberwachung, Magdeburg
- Werkstattplanung
- Form TL, Radolfzell