Paul Schmidt: 'We are convinced of straw and that’s why we recommend it'
Natural materials are at the top of the list at Atelier Schmidt when it comes to new buildings and renovations. We talked to Paul Schmidt about the sense and benefits of various natural building methods.
In the story of the three little pigs settling down, the straw house collapsed when the wolf started to blow on it, the wooden house also failed, and only the one made of stone passed the test. If Joseph Jacobs, or Elizabeth Shaw who later wrote the German version, were to rewrite the story today, they would probably have to apply different standards. Whereas building with straw at the time of the story's origin stood for ease and comfort, and building with stone for industrious and hard work, the situation today is quite different. Building with wood and straw, and with natural materials in general, is experiencing an ever-increasing demand. Building with stone — or, in contemporary terms, concrete — is under discussion because too much CO₂ is produced during the manufacturing process. All major cement manufacturers are working on more economical formulas and substitutes, as are researchers at universities and colleges. And while timber construction has been gaining ground on the market for decades and Anna Heringer postulates building with clay, the planners from Atelier Schmidt in Truns, Switzerland, advocate building with straw.
Paul Schmidt: We usually deal with two different types of clients: Some have heard about our straw buildings and are fascinated by the possibilities. Others come from the area where our office is based and simply like our architecture. I find it very exciting to build with locals, because you still have to convince them of this construction method.
Our arguments for sustainable building are always the three factors of energy input during production, operating energy consumption, and service life. In detail, this means that we seek to build as ecologically as possible, then consume little energy during operation, i.e. avoid mechanical solutions wherever possible, and construct an aesthetic building that has a very long lifespan thanks to its adaptability. We also say, think of a monastery: The Disentis Monastery, for example, dates back to the late 17th century, but it was so well designed at the time that it can still be used now and serves all needs.
In our projects we therefore want to consider all three aspects — straw is only a means to an end. It allows us to reduce the amount of energy required of production and operation. That is what convinces most people and they understand that it is necessary to build ecologically. Whether you then build with straw or sheep's wool is secondary. Nevertheless, I also understand the perception from the outside that we are a “straw-building” family.
We generally do not tell the client what to do. However, we are convinced of straw as a product and that's why we recommend it. On the other hand, we worked with sheep's wool when converting a sheep farmer's house. His house is a solid timber building, the appearance of which we wanted to preserve. Straw would have had to be placed on the outside, thus hiding the timber construction, but we were able to insulate with wool on the inside.
Although wool is a good insulation material, sheep are primarily kept for landscape maintenance and meat production, and their wool is often discarded. Some companies use it to produce insulation material, but that costs more than straw because the wool has to be processed into a building product. We also want to create economical buildings, of course.
Exactly. Our buildings can be as expensive as timber buildings, but they must not be more expensive than conventional buildings. Otherwise, customers will back out of the project. It is a great challenge to construct an ecological building under these premises and to stay within the same cost range.
I recently made a comparison in a tender: For a timber building with a wall thickness of 36cm, we asked for a quotation for the delivery and installation of small straw bales and were offered a price of 55 francs per square meter of straw bale installed. For comparison, we considered glass wool, which in itself is inexpensive. With the same wall thickness, glass wool costs about 70 francs per square meter delivered and installed! When analyzing the insulation materials we have already worked with — isofloc, wood wool, glass wool, rock wool, sheep wool — we came to the conclusion that the advantages of straw are simply unbeatable by comparison.
To date, production and durability have unfortunately not played a role in these programm. In Switzerland, a house can theoretically be insulated with EPS or XPS and have comfort ventilation — and is awarded a Minergie label. Another example: There are now sanitary systems producers who want to recover residual heat from a building's waste water using complicated processes. In this area, with this focus alone, that may be an approach. But even here, the operating energy use is closely scrutinized. In the overall view, this approach is wrong. The manufacturing energy and the lifespan are much more important.
Even though this is the case, one must not neglect the energy needed for processing these materials and transport costs. Straw is available in large quantities in most areas, the logistics for it are even provided by agriculture — not by the construction industry! — and it is inexpensive. You can of course look for insulation materials along Spanish coasts, but I think it would make more sense to use the obvious. Straw should be used much more widely today because it meets all the criteria.
This is happening, but it's still too little. About a year ago, Herzog & de Meuron called us in as expert planners for a project. The office had made an elaborate analysis of many known insulation materials to find out how to insulate buildings as sustainably as possible. In the analysis, they came to the conclusion that straw is well suited for continuing work.
Weighing up the ecological and economic aspects, it was decided to insulate the roof with straw and the walls and floor with cellulose. Small straw bales are about 36cm thick and are well suited for installation in a wooden element wall. If the wall thickness is smaller, the straw bales can no longer be used directly from the field. In that case, the bales have to be cut open and the straw needs to be chopped so that it can be used as blow-in insulation. In this comparison, cellulose was more economical. In another project, we have worked with rock wool for fire protection reasons. The distance between the buildings did not comply with the standard. Each project has to be considered individually.
We have already used straw as a load-bearing material in various projects. But here, too, we are confronted with the problem already mentioned: Margins are low, the construction industry has little interest in such products, and it is difficult to find companies that are willing to do the execution. There are companies in the EU area that offer standardized construction straw bales according to DIN. In the end, it is straw from the fields, but it is blown out and thus cleaner. It is, however, also about 50% more expensive. In terms of market economy, interest in this is low — after all, the product already exists and you can only make it more expensive artificially.
Of course, we do not turn a blind eye to the present day! In terms of waterproofing, petroleum products are a blessing, because you don't have to be as consistent about water protection. Foundations are mostly made of concrete, because that makes sense from an economic point of view. In our project in Nänikon, too, we decided to build a waterproof concrete tank (white tank) rather than one using bitumen waterproofing (black tank). We did this because it is more ecological. This is because the consequence of non-waterproof R-concrete is a higher energy input during production, as we have to use bitumen.
If the budget were not an issue, buildings could be constructed as they were in the past: as solid timber structures on a quarry stone foundation. Although, from the point of view of operating energy consumption, we would no longer put a solid timber building on top of the foundation but rather a timber-straw structure, so that energy input for both production and operation remains low.
The buildings in Nänikon are an investor project, and we were able to achieve a market-compliant return with sustainable construction! This proves that investor development can also be carried out in this way. For these projects, you need clients who think outside the box and are satisfied with a somewhat lower net return. If I clad buildings with EPS/XPS, the return is higher in the short term — but this won't serve future generations.
Let me say this again: If it were regulated by law that the focus of subsidies is not on operation, but that the energy used for production is also essential, different results would emerge. What if someone who constructs a building using a lot of energy for its production is subsequently forced to compensate by reducing operating energy use much further? Artificial insulation materials would become uninteresting. Things have to change on the legal side. In Germany, the government under Olaf Scholz has suspended the subsidies and wants to reorganize them. The focus should move away from operating energy consumption, and energy input for production should also be included in the assessment of a project. As long as we play in a market that is unfair from nature's point of view, where sustainable building products compete with non-sustainable ones, building owners will prefer six percent net yield to four percent.
It is already very difficult to find a good way and to create awareness for different building methods, even among large investors. That's why I also believe that the best approach here is to equate energy input for production with operating energy consumption when assessing ecological values.
Ultimately, we should build houses that are locally rooted and allow for many uses so that their lifespan is as long as possible. Fortunately, none of our buildings have been demolished so far — our goal is that a house can stand for several hundred years if possible. Then it is sustainable. Otherwise it isn't.
Thank you very much for the interview.
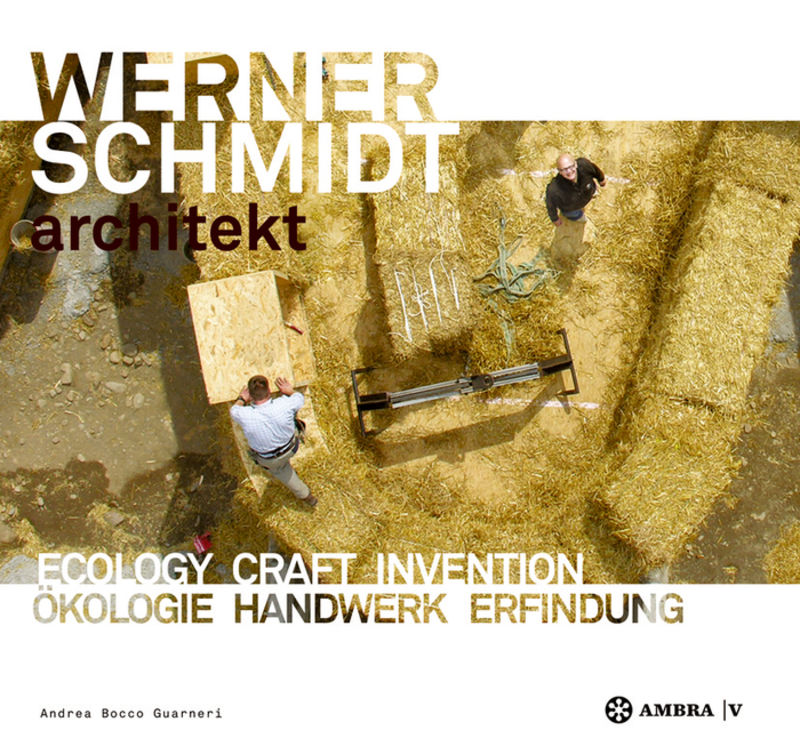
WERNER SCHMIDT architekt
Andrea Bocco Guarneri (ed.)
23 x 21cm
288 Seiten
616 Illustrationen
Hardcover
ISBN ISBN 9783990435052
Birkhäuser Verlag
Dieses Buch kaufen